Building Momentum
By Emily Thurlow
With the federal COVID-19 public-health declaration coming to an end this past May, the once-global pandemic may seem all but a distant memory. For many businesses, however, its impact certainly hasn’t vanished from sight.
Challenges in obtaining materials and equipment continue to vex general contractors in the construction industry in Western Mass. and across the nation. This extended period of uncertainty — in both duration and scope — has left many feeling uncertain about the future beyond 2023, but there are positive signs, too.
Rising building costs and higher interest rates have been of particular concern to Kevin Perrier, president and CEO of Five Star Building Corp. After work in the Easthampton company’s largest sector — aviation — was essentially grounded for the past two years, Perrier says he was expecting business to be on the slower side.
But to his pleasant surprise, he was wrong. Quite wrong.
“We really saw the aviation sector rebound this year. It makes up for essentially two years of no growth and no construction,” he said. “Honestly, this was one of our busiest years I can remember.”
And Five Star isn’t alone. In fact, despite ongoing resource constraints, construction firms like Laplante Construction Inc. in East Longmeadow and Sweitzer Construction LLC in Monson are reporting an increase in the volume of their work, while Fontaine Bros. Inc. in Springfield calls 2023 the firm’s best-ever year for revenue.
“We really saw the aviation sector rebound this year. It makes up for essentially two years of no growth and no construction. Honestly, this was one of our busiest years I can remember.”
“This year has been good. It’s been steady,” said David Fontaine Jr., CEO of Fontaine Bros. “I think our efforts to work really hard to deliver our projects on time and on budget have really strengthened our relationships with our clients because they’ve seen that we’re still getting things done, successfully, no matter how difficult the climate is.”
Reflecting back on those unprecedented times, BusinessWest spoke with several companies in the region who shared how they have been constantly rolling with the punches by being as strategic as possible when planning out projects and seeking alternatives in design, materials, or vendors when applicable, and, above all, maintaining the safety of everyone involved.
Gaining Altitude
Within two weeks of the national shutdowns to stop the spread of COVID-19 in March 2020, Perrier estimates that Five Star lost “millions upon millions of dollars worth of work.” Initially, projects were put on a temporary hold, but shortly thereafter, the majority of those projects were canceled, he said.
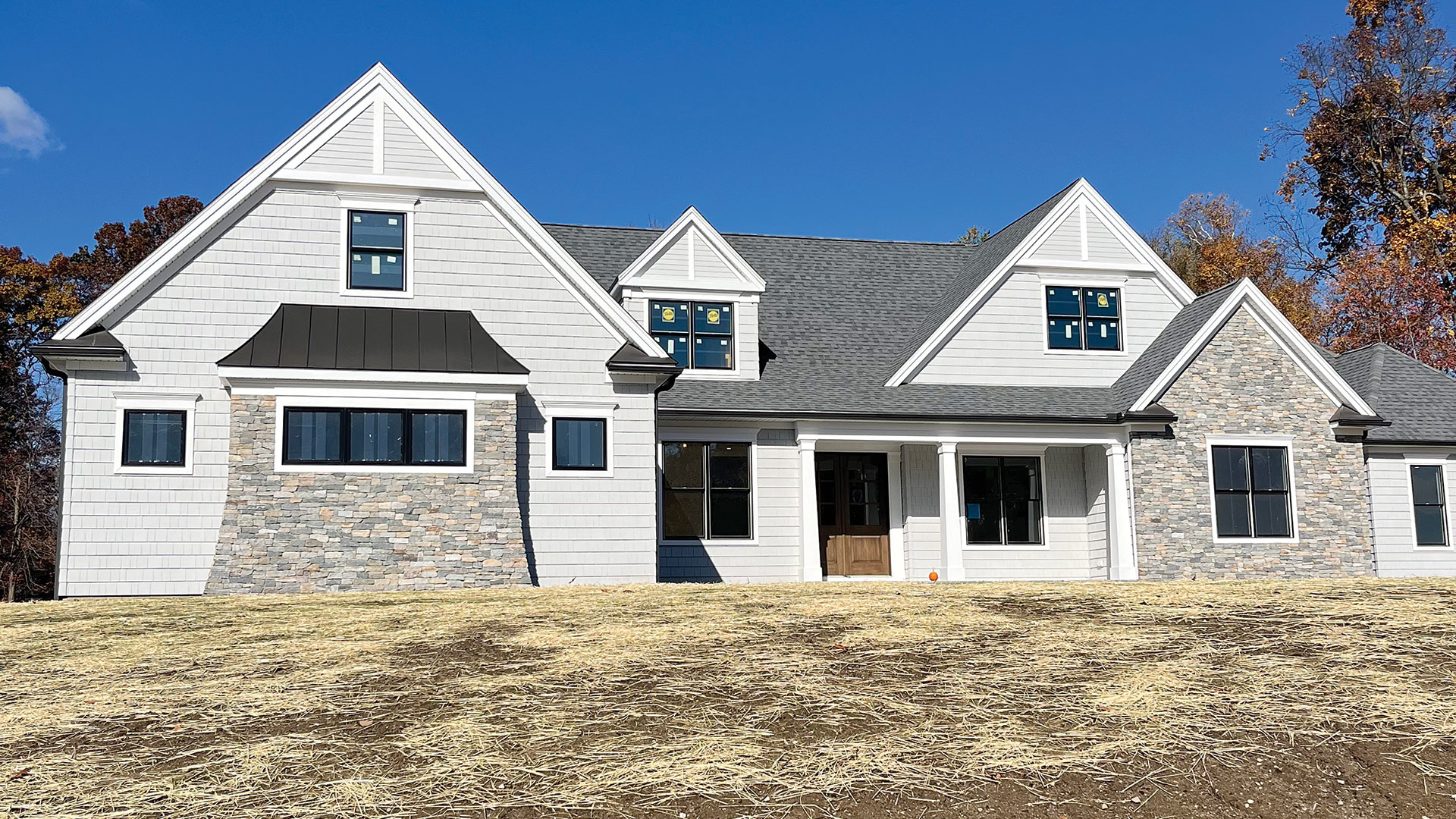
Laplante Construction recently completed this new home build in East Longmeadow.
This year, the company, which has been working up and down the East Coast in the aviation sector for the past 13 years, has more than made up for that lost time working with clients like Delta Air Lines and HMSHost International, a U.S. highway and airport food and beverage service company that is a subsidiary of the Italian company Autogrill SpA.
Some of the projects Five Star has completed include the new Gachi Sushi House in Terminal C at Boston Logan International Airport, as well as a Hudson store, offering food, beverages, and travel amenities, in the Terminal B/C connector, and a Hudson Nonstop at Charleston International Airport in South Carolina.
More recent projects underway at Logan include a new hangar roof for Delta Air Lines, some infrastructure work in the lower levels of the airport, and building the new Fox & Flight Restaurant in Terminal A for travel retailer and restaurateur Paradies Lagardère. Perrier said the new restaurant is slated to be the largest restaurant at the airport.
“I think our efforts to work really hard to deliver our projects on time and on budget have really strengthened our relationships with our clients because they’ve seen that we’re still getting things done, successfully, no matter how difficult the climate is.”
“At any given time, we usually have six to 12 projects going in the aviation sector, primarily at Logan,” he said. “The new Terminal E expansion at Logan kept us very busy; it generated quite a bit of work for us to the point that we were actually turning down bids out there. We just kind of reached our capacity for the summer because it was such a push all at once.”
Combined with several mixed-use projects, Five Star had its hands full, he added.
Meanwhile, Laplante Construction and Fontaine Bros. also share glowing reports for their work in the residential and commercial sectors, respectively.
Since expanding his business three years ago to Cape Cod, specializing in mid- to high-end home building and remodeling, Bill Laplante, president of Laplante Construction, says he hasn’t seen any kind of slowdown as a result of increased interest rates. Approximately 80% of the company’s business involves residential projects.
“So the Cape market has been very, very good. There’s an awful lot of work out there,” he said. “I just think there are fewer people out there that are relying on mortgages and are self-financing, or they’re paying cash for work to be done out there.”
For Fontaine Bros., projects that have been publicly funded have remained more consistent than privately funded or developer-driven projects.
Recently, the company completed the three-story DeBerry-Swan Elementary School project on Union Street in Springfield, which opened in the fall. Fontaine is also currently working on school-building projects in Westfield, Worcester, Tyngsboro, Walpole, Fitchburg, and East Brookfield, as well as the UMass Amherst campus.
Pat Sweitzer, operations manager of Sweitzer Construction, also described 2023 as an especially good year. She said that she and her husband, Craig Sweitzer, who co-own and operate the company, attribute this year’s successes to their employees and partners.
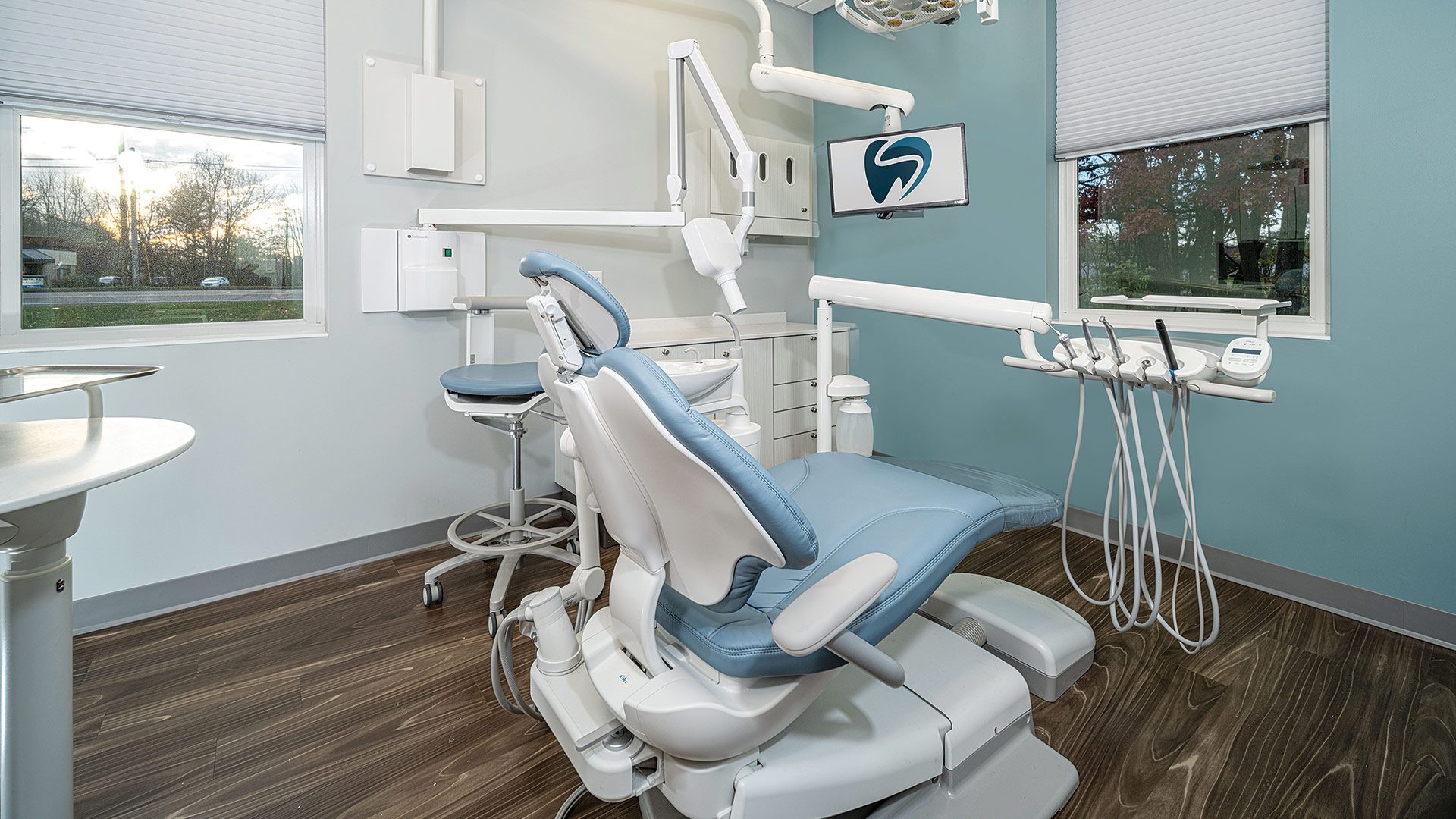
Sweitzer Construction has developed an expertise in dental-office construction, including this project for Alliance Dental Care in East Longmeadow.
Pat also offered praise to her sons, Brian and Michael Sweitzer, as both have taken on leadership roles as the firm is in the process of transitioning into a second-generation company.
On the smaller end of projects, the company repaired some buildings at Smith College’s campus and built a new dental office at 265 Benton Dr. in East Longmeadow. One of the larger projects on the company’s docket this year was the conversion of a 19th-century mill building in Northampton into Cambium Analytica’s safety-compliance lab for cannabis products. The new sterile testing lab, which hasn’t opened yet, is located at 320 Riverside Dr., at the site of the former Northampton Cutlery Co.
“Taking a former very old factory building and turning it into a sterile testing lab … the outcome is just remarkable,” Sweitzer said.
Mark Sullivan, president and executive project manager for D.A. Sullivan & Sons Inc., called 2023 the Northampton company’s “first normal year” in several years, adding that things started to stabilize, in a post-COVID sense, during the second half of 2022, and that momentum has carried through 2023.
Strength Amid Challenges
While supply-chain issues have dramatically improved across the board since the middle of the pandemic, almost every contractor BusinessWest spoke to has highlighted challenges with electrical components and equipment like meter sockets, switch gears, generators, and transformers. The demand for transformers has been exacerbated by the lack of available domestic manufacturers to meet the increased need.
“Some of those electrical items still have ridiculously long lead times,” Laplante said. “We built a house — literally finished the house a year and a half ago — and there was supposed to be a ground-mounted transformer for the electric service to the house, and they didn’t have them.”
While waiting for the transformer to come in, he said the electric company has supplied the customer with temporary power. “That transformer has been on back order for a year and a half, and we probably won’t see it for another year. When it comes in, we’ll swap it out.”
For the most part, customers have remained understanding, he added. Other materials that continue to be difficult to source in a timely manner include mechanical equipment, like rooftop units for healing and cooling equipment.
“It seems like anything that has a manufacturing process that has a lot of little pieces and parts that are coming from all over continues to be difficult,” Fontaine said. “And for things like, say, a chiller or a piece of switchgear, they won’t start the manufacturing process until they have every little piece or part of what they need at the facility where they put it together.”
Highlighting a similar concern, Sweitzer said her company has made efforts to order products ahead of time. On Nov. 28, a groundbreaking ceremony was held for one of its projects, Embr Springfield, a $2 million dispensary on Boston Road. At nearly the same time, Sweitzer Construction was ordering the rooftop heating and cooling unit.
“We’re just digging the foundation now, and we already ordered the rooftop unit because it will take that long for it to come in,” she said. “The long lead times are a challenge.”
Sullivan noted that, because lead times for electrical components and mechanical equipment are still driving the overall work schedule for D.A. Sullivan & Sons, the firm’s focus has been on pre-construction services and identifying items they feel may trip up their plans.
Another niche facing long lead times is luxury appliance brands like Wolf and Sub-Zero, according to Laplante. Under current lead times, both brands are averaging roughly 12 months to arrive once ordered. Similar to the transformer problem, Laplante said both manufacturers are providing small, temporary refrigerators until the one that was ordered arrives.
“A lot of the appliance companies and the manufacturers are doing the best they can to provide a temporary fix until the final product is delivered,” he said.
View to the Future
As the end of the year beckons, many of the companies BusinessWest spoke to are feeling cautiously optimistic about 2024.
Sweitzer has a number of projects on the books, including a few with new partnerships with other contractors like Kleeberg Sheet Metal Inc. in Ludlow.
Sullivan said his firm is wrapping up some municipal work and starting some new projects at libraries, fire stations, and safety complexes, and even has a few projects at local universities and colleges in the queue for next year.
“Next year and beyond, we have the biggest backlog we’ve had in over 10 years,” he said.
Meanwhile, Fontaine Bros. has secured a healthy amount of public-education work for next year and is positioning itself to be ready for other projects on the horizon.
“I think, generally speaking, the industry is always changing. It’s always exciting,” Fontaine said. “It’s been a challenging couple of years, for sure, but it’s something new and exciting to wake up to every day, and we’re thankful that we’ve continued to be able to be successful through it. So hopefully, 2024 and on will get easier, but whatever happens, we’ll be ready to tackle it.”
Though the residential trend of smaller luxury homes looks to continue, Laplante said there are also a number of very large-scale luxury home builds on the books.
“We’ve seen people downsize and go from a large, two-story home to a high-end, smaller ranch with very, very nice amenities on one-floor living, but interestingly enough, we also have some very large homes in the pipeline for next year,” he said. “This is particularly interesting because, generally speaking, over the last five years, there’s been a trend to reduce the overall size of the homes that are being built to single-story living.”
As for Five Star, Perrier says the new year still holds a lot of question marks for him as the aviation sector tends to be a little more unpredictable. Though there are infrastructure and retail build-out projects on the books, higher fuel costs and tightening budgets can often bump jobs at the last second, he explained.
“What tomorrow brings, I don’t know. I guess I’m still going in with the same hesitation I had for 2023,” he said. “Hopefully, I’ll be pleasantly surprised again.”